Sign up to be notified of our new blog posts.
The Value of Custom-Built Processing Equipment…and What to Do If You Can’t Wait
Posted on March 09, 2022
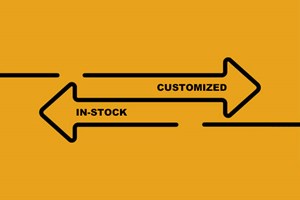
Manufacturers that need processing equipment may have faced a similar challenge lately. While most would prefer equipment customized to their operation and product, some may feel they need to seek other options, like in-stock or used equipment. The long-term nature of processing equipment makes this a particularly important decision point: a high-quality production vessel can operate for decades.
Most Frequently Customized Vessel Elements
If you find yourself in such a position, it would be helpful to consider the equipment elements that process manufacturers most frequently want to customize.
- Capacity: Perhaps the most obvious equipment customization is the size of your production vessel. Not only do you need to consider your short- and long-term production volume needs, but you must also synch vessel capacity with the rest of your workflow; for example, how the capacity of your downstream filling equipment will impact how much product volume you can discharge.
- Vessel jacketing area: The surface coverage of the jacketed area of your production vessels can drastically affect heat-up and cool-down times, which can affect the overall time needed for a batch to process. Custom vessels can maximize efficiency by configuring the jacketed area to the ideal heating and cooling needs of the product or products being processed.
- Agitator system: The agitator system is often among the highest priorities for manufacturers to customize, given the impact it has on quality control, product consistency and production efficiency. Your product’s characteristics—e.g., weight and viscosity, ingredient miscibility, ingredient properties—will dictate the type of mixing solution best suited for your needs, along with operational factors like your production workload and power access. Here is a helpful article for more on finding the right agitator for your operation.
- Surface finishes: Sanitary requirements can mean that a vessel’s surface finish can directly affect whether the vessel can be used for certain products. Even in applications that don’t require a sanitary or mirror finish, a higher-grade finish can make it easier to discharge product and clean the vessel, which can increase yield and accelerate turnaround times.
- Efficiency features: Depending on your product, some equipment features can have a significant impact on operational efficiency. These include Clean in Place (CIP) systems, coil-wrapped vessel jackets and sanitary ball valves, each of which can be invaluable in certain situations.
- Extra features: Cover lift assists and cover grates for vessels, and Variable Frequency Drive and motor cutoff safety switches for agitators are commonly requested features.
Options When Custom-Built Isn’t An Option
Thanks to the elements mentioned above, custom processing equipment has clear advantages that can be critically important to your production efficiency and product quality—even if you must wait longer than you’d like. But what if you have an urgent need that just can’t wait for a custom build? Here are some options:
- In-Stock inventory: Some manufacturers keep a supply of equipment in-stock. This is typically limited to standard sizes and feature sets, which—if your application doesn’t present any unique or challenging mixing requirements—may be adequate for you. However, in this current short supply/high demand environment, much of that inventory has dried up.
- Used equipment: Given the long use-life of high-quality equipment, there is almost always a robust used market available (many Lee Industries vessels manufactured over 40 years ago are still running strong!). But these days, be prepared to pay almost as much for a used vessel as you would for a new, custom-built vessel. If you do find a used vessel of interest, you simply must do your due diligence on its use and repair history; otherwise, you could be taking on a big risk. Use this guide to the questions you should ask when buying a used vessel.
- Service or modify existing equipment: If you have an existing vessel that isn’t doing enough to meet your needs, you could likely get more out of it by scheduling a thorough service visit by a certified ASME Code Technician and Inspector. Services like jacket leak repair, agitator shaft alignment, agitator rebuild, vessel refinishing, and replacement of bearings or bushings in the drive, gearbox and motor can greatly improve equipment performance.
Similarly, you may be able to upgrade your existing equipment—or an in-stock or used vessel you find—with new features or functionality that can help you meet your production need. This can include agitator upgrade, CIP spray ball installation, adding sensing and control instrumentation or other high-impact modifications.Lee Industries technicians service all types of vessels, including equipment from other manufacturers. Click here to schedule service or modifications.
Your processing equipment is the core of your operation, so you want to make the best choices for both the short- and long-term. By considering all your options and factoring in your specific product and situation, you can make the right decision for your operation.
For more information, or to discuss your situation, reach out to one of our Application Engineers. We’d be happy to help.
Comments
Add Your Own Comment