Sign up to be notified of our new blog posts.
Ramping Up Cosmetic Production
Posted on July 19, 2023
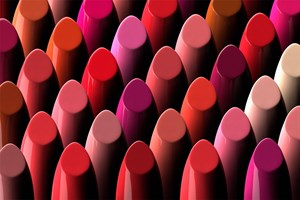
With growth spurred by demand for “clean beauty” and “organic makeup” products and a rising focus on inclusivity, today’s cosmetics and personal care industries are being transformed by a wave of independent and start-up manufacturers. For many of these manufacturers, the migration from small-batch lab production to larger-scale processing can be a challenge.
That’s because ramping up production isn’t as simple as multiplying the amount of ingredients required for the higher volume. Many ingredients used in cosmetic, skin care and personal care products behave unpredictably when produced in larger batches. For example, carbohydrate- and plant-based ingredients, preservatives, electrolytes and other ingredients do not react the same way when mixed in larger quantities as they do in small quantities. Furthermore, the size of the production mixing vessels needed to produce larger quantities—and their performance characteristics—can require different mixing, heating and cooling processes than those used to produce small-batches.
If you’re considering ramping up production of your cosmetic or personal care product, here are some of the process- and product-related factors you should consider:
Process-Related Issues that Affect Cosmetic & Personal Care Product Production at Larger Quantities
As you scale to larger batches, you must also carefully consider every aspect of your process. Here are some of the most important process-related factors:
- Heating and cooling times will vary widely from a small, five-pound batch produced in the lab to a 50-pound pilot batch, and then to a 500-pound production batch. This may have an impact on the desired characteristics of your product, and its heating and cooling profiles may need to be altered in larger batch sizes to meet your product requirements.
- Ingredient application will change from lab to production floor. Since adding a pound of a seed butter ingredient in a lab mixer is much easier than adding a 100-pound block of the same ingredient into a production mixing vessel, you must carefully consider the additional ingredient processing steps (e.g., cutting, pre-mixing or specialized loading) that must be used in production. Additionally, changing the order of how ingredients are added to the larger production batch may impact the characteristics of the final product.
- pH levels are critically important for most cosmetic, skin care and other personal care products, and levels which are either too low or too high can have a significant impact on the product’s safety, efficacy, color and other important characteristics. Because of this, pH levels must be monitored at every step of the process and adjusted as needed for larger batch sizes.
- If pre-mix vessels are used, they can impact both scaling and ongoing production operations. Some cosmetic and personal care products processors deploy a series of smaller vessels to pre-mix key components of their formulations. For example, they might use one pre-mix vessel for mixing color ingredients and another for mixing fragrances, before adding those components to the main oil/water emulsion base in the main vessel. This approach can allow for each pre-mix to be closely monitored and tested for consistency and other characteristics before the final mixing process.
- Pipelines and pumping systems used in the vessel discharge process may also influence larger production batches, requiring upstream or downstream changes to vessel loading, discharge and distribution systems.
Product-Related Characteristics that Affect Cosmetic & Personal Care Product Mixing as Production Scales
Many cosmetic and personal care products are emulsions of oils mixed with water and other ingredients, so high-shear mixers are often used for mixing. High-shear mixers break down these oil-based ingredients to achieve stable, uniform mixing consistency throughout the batch.
But your product’s mixing dynamics can change—considerably in some cases—as you scale from lab to small or pilot production to large production volumes. This is due to the mixing, heating and cooling characteristics of larger production vessels compared to smaller lab mixers. For example, a larger vessel will have different dispersion times and characteristics than a smaller bench mixer and may take longer to heat and cool. Such variances can affect the attributes of your product.
Therefore, to achieve the product characteristics you want at production scale, you must determine the mixing system that can best produce them. Product factors to consider include:
- Particle size: Knowing the desired particle size of your new product formulation is an important factor in determining what type, size, power level and configuration of mixer will be required for production batch sizes. Knowing your target particle size can also prevent overspending for a mixing vessel that is too powerful for your needs. Most importantly, knowing and testing particle size is critical to assuring consistency in and between lab-created and scaled production batches. If you’re not already doing so, use a laser diffraction analyzer to get reliable particle size measurements.
- Rheology: The rheological properties of your lab-produced product—which determine how your product flows and deforms against stress and time—are important data inputs for designing the mixing system you’ll need to produce the product at scale. This is particularly so for cosmetic, skin care and personal care products, which use modifiers like thickeners and texturants, or may include actives or botanicals. These additions can complicate the ability to consistently maintain skin feel, handling and stability characteristics at larger production volumes.
- Viscosity: Similarly, it is important to know the desired viscosity for your product, which is dictated by its purpose. For example, the viscosity of lotions that form a protective layer on the skin will vary from those formulated to penetrate the skin quickly. Once you achieve your ideal viscosity level in the lab, you can use that as a target to determine the agitation style and power your mixing system will need to produce at scale. Viscosity is measured in Centipoise (cPs) and can range from one (water) to more than 1,000,000.
Making the leap from small-batch to production scale can be challenging, but with enough attention to these key process- and product-related factors, you should have no problem making the jump.
For more information, or to discuss your process with a Lee Industries Applications Engineer, just contact us. We would be glad to help.
Comments
Add Your Own Comment