Sign up to be notified of our new blog posts.
Do These Three Things Before Putting a Used Processing Vessel into Active Production
Posted on April 06, 2022
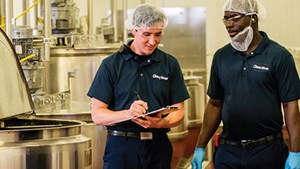
The market for used processing vessels is typically strong, due in large part to the long use life of high-quality equipment. We often see processors still using a vessel we built over 50 years ago, for example. That, and today’s high demand for new equipment, is leading even more processors to buy used equipment.
But processors must avoid rushing a newly acquired used vessel into production, lest they take on some potentially costly risks. Taking these three steps first—prior to activation—will go a long way to ensuring operational efficiency.
1) Verify the vessel’s use and service history.
Knowing the history of your vessel is important to your operation’s safety and liability. This applies to the vessel’s past use and its maintenance records.
As far as use history, it is most important to know the ingredients that have been processed in the vessel. You want to be sure that there are no cross-contamination issues that would affect your product. For example, a vessel that had been used to mix hazardous chemicals should not be used for food processing. Follow the entire chain of ownership, not just the original owners, to gain a clear understanding of any issues you need to address.
Service history is also important. Processing vessels with steam and water jackets are considered “unfired pressure vessels” under A.S.M.E. code, so all A.S.M.E. guidelines must be followed and documented for any inspections, repairs or alterations. Operating the vessel without this documentation can open your company up to significant liability.
2) Identify necessary modifications.
Most vessels on the used market were custom-built for their original owners with specific features and operating characteristics. As a result, your used vessel may need to be adapted to optimize efficiency for your production.
Common modifications can include the addition of connections, agitator design enhancements (i.e. scraper materials), valve design changes, and the integration of features such as covers, cover lift assists or grate assemblies.
3) Perform preventive maintenance and stock spare parts.
The most important step you can take to ensure production continuity with your newly acquired used vessel is to conduct preventive maintenance before putting the vessel into production. Most used equipment dealers don’t perform maintenance on the vessels in their inventory, so this step is essential to avoid costly downtime.At a minimum, preventive maintenance includes inspecting your vessel’s jacket integrity to identify and repair leaks, checking agitator shaft alignment and drive for bent or misaligned equipment, and replacing worn bearings or bushings in the gearbox or drive motor.
This preventive maintenance is necessary before you put your used vessel into production, but keeping an inventory of appropriate parts on-site will ensure you minimize downtime for repairs. This is particularly important for used equipment, as it is often sold without a warranty. Parts to keep on-hand include commonly worn components like scraper blades and pins, O-ring seals, drive shaft bearings, seals and ball valve seal kits, all of which should be replaced on a regular schedule.
Once these three steps are completed, your newly acquired used vessel will be ready to produce for you. If you need help getting to that point, Lee Industries can help. Our application engineers can discuss modification options and our A.S.M.E. certified technicians can inspect, repair and service most vessels. We also offer a full range of vessel replacement parts. Just contact us to review your situation.
For more help determining the right equipment path for your operation, read New or Used Kettle? How to Make the Right Choice for Your Food Processing Operation.
Comments
Add Your Own Comment