Sign up to be notified of our new blog posts.
Vacuum De-Aeration: Removing Trapped Air Bubbles for Uniform Product Consistency and Accurate Dosing
Posted on June 15, 2022
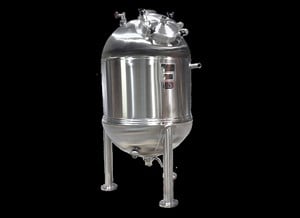
Manufacturers who process high-viscosity products such as creams, lotions, ointments or gels often encounter problems with air bubbles forming in the batch, as air becomes entrained in the product during agitation.
These unwanted air bubbles can prevent exact measurement and dispensing of the product in its end-use packaging, a particular problem in bio-pharma products, where highly precise dosage amounts are often required for safe and effective patient treatment.
How vacuum de-aeration works
Vacuum de-aeration is a process that removes air bubbles by pulling the trapped air out of the batch. In a vessel equipped for vacuum operation, air bubbles can be eliminated either by mixing ingredients under a vacuum, which prevents air from becoming entrained in the mixture, or by pulling a vacuum on the vessel after the mixing process.It is possible for excess foam buildup to occur during the vacuum de-aeration process. This happens when air trapped in the batch is pulled by vacuum and attempts to break the surface tension at the top of the batch, forming a mass of bubbles that foam at the top of the vessel. This unwanted product foaming can cause additional problems if it moves up through the vacuum line and into the vacuum pump, contaminating these parts of the vessel.
Designing your vessel to prevent foaming
To prevent foaming:
Vacuum can be manually adjusted as needed using a valve on the vacuum port to normalize air pressure in the vessel.
This air, when introduced into the top of the vessel:
- Causes the bubbles in the foam to pop
- Reduces the level of foam in the vessel.
- As these bubbles pop, they release additional air which can then be removed by applying more vacuum.
The manual valve can be adjusted or throttled as needed to reduce the air and foaming inside the vessel, until the foaming stops, and all the air is pulled out of the batch.
NOTE: Because of this situation, consider how much air space you’ll need at the top of your vessel to accommodate the foaming and vapor release that occurs during vacuum de-aeration. In your vessel design stage, be sure to allow for additional space above the working level of your vessel to eliminate the potential for excess foam buildup to enter the vacuum port line and vacuum pump.
Vacuum de-aeration is critical for applications with exact dispensing requirements
For dosage-critical products, eliminating air bubbles through vacuum de-aeration is necessary to accurately dispense the precise amounts required in final product packaging. This is especially important when dispensing exact amounts into packaged bio-pharma products to be administered to patients in medical applications.For more information on vacuum processing for biopharma, personal care, chemical or other products, reach out to a Lee Industries Applications Engineer. We’re happy to review your application and help you design the processing vessel solution that fits your needs.
Comments
Add Your Own Comment